
Design of Remote Control Drone for Agricultural using Flight Controller to Reduce Pesticide Damage
Copyright ⓒ 2021 The Digital Contents Society
This is an Open Access article distributed under the terms of the Creative Commons Attribution Non-CommercialLicense(http://creativecommons.org/licenses/by-nc/3.0/) which permits unrestricted non-commercial use, distribution, and reproduction in any medium, provided the original work is properly cited.
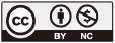
Abstract
Crop cultivation in greenhouses to improve crop productivity is increasing. We designed a small and lightweight agricultural drone to prevent poisoning accidents during pest control in greenhouses. In order for the drone to be able to fly in the greenhouse, we designed a drone measuring 600 mm in length and 300 mm in height and simulated the possibility of flight using e-calc. As a result, a sufficient flight time of 6.9 minutes was secured for drone weighing less than 4,200 g. However, the drone weighing 4,200 g caused a small difference between the thrust used for hovering and the thrust used in flight, and it was predicted that flight would be impossible. Therefore, to operate drones stably in greenhouses, it is desirable to manufacture the drone with a weight of 4,000 g or less.
초록
농작물의 생산성 향상을 위해서 시설하우스에서의 농작물 재배가 늘어나고 있다. 시설하우스내에서의 농약 방제 시 중독 사고를 예방하기 위하여 소형 경량의 농업용 드론을 설계하였다. 시설하우스 내에서 비행을 할 수 있도록 기체 길이 600mm, 높이 300mm의 기체를 설계하여 비행 가능성을 e-calc를 사용하여 시뮬레이션을 시행하였다. 그 결과, 기체 무게 4,200g 이하일 경우 최소 비행 시간이 6.9분으로 충분한 비행시간이 확보되었다. 하지만 기체 무게 4,200g에서는 호버링에 사용되는 추력과 비행 시 추력의 차이가 작아 비행이 불가능할 것으로 예측되었다. 시설하우스내에서 드론을 안정적으로 운행하기 위해서는 기체 무게를 4,000g 이하로 제작하여야 할 것이다.
Keywords:
Drone, Flight Controller, Remote Control, Pesticide Damage, Green House키워드:
드론, 비행 제어기, 원격 조종, 농약 피해, 시설하우스Ⅰ. Introduction
The domestic agricultural industry has increased production through the Green Revolution, and has been steadily developing and increasing production after the White Revolution using greenhouses. In particular, the advent of smart farms based on information and communication technologies, such as, the internet of things (IoT) and information and communications technology (ICT), is accelerating the growth of the agricultural industry. However, with the development of medical care, and science and technology, the average life expectancy of humans is increasing, which is driving the aging of agriculture. Automated smart farms can improve working velocity and efficiency, which can be a solution to the growing number of elderly farmers. Accordingly, research on smart farms has recently been conducted in various ways to solve the problem of increasing production and aging [1-4]. To increase crop production, pest control must be actively carried out using pesticides. Many automated agricultural machines are being developed due to the declining and aging farmers’ population. Many studies are being conducted to allow drones to be used in various industries as they can be steered by wireless radio waves [5-7]. Recently, various attempts to use drones in the agricultural field have been studied [8-10]. However, Although drones are cheaper than unmanned helicopters in terms of price and operating costs, drone also have the disadvantage of short flight times [11]. Also drones for pest control are manufactured to be suitable for large-scale agricultural areas, and have large fuselages and heavy weight, limiting their use by elderly farmers. Also, greenhouses, such as, smart farms are small in size, making it impossible for large drones to fly, and these drones could damage the exterior walls which are made of vinyl or glass. Because of this, farmers are often unable to use drones and control pest themselves in the greenhouse, hence they are exposed to pesticide poisoning accidents. Therefore, to control pest in greenhouses, the drone must be smaller in size, light in weight, and capable of long-distance control.
In this study, to prevent pesticide poisoning in greenhouses, we conducted a manufacturing simulation of a small and lightweight drone and analyzed the possibility of flight.
Ⅱ. Drone Configuration
The drone used in the greenhouse is divided into the fuselage, injection unit, and power supply unit, and the total weight of the drone has a great influence on lift and thrust.
Therefore, it is necessary to confirm whether the flight is possible by reflecting the actual expected weight at the time of design. Figure 1 shows the structure diagram of the drone. To reflect the weight at the time of simulation design, we selected the main parts of the fuselage, injection unit, and power supply unit, and measured their actual weight.
The fuselage is composed of a control unit including the outer shape of the fuselage and various sensors. The fuselage is usually made of carbon plates and carbon pipes to reduce weight. The control unit includes various sensors and propellers, such as, the flight controller (FC) for controlling the drone, the global navigation satellite system (GNSS) for grasping the current position and movement path, the brushless DC (BLDC) motor for turning the propeller, the electronic speed controller (ESC) for controlling the velocity of the motor, and the light detection and ranging (LIDAR) for searching the periphery. Various sensors, such as, FC (Pixhawk v5 nano, CUAV Co., Ltd., China), GNSS (Here+ RTK, HEX Co., Ltd., China), BLDC (Antigravity MN4006 KV380, Tmotor Co., Ltd., China), ESC (Alpha 40a esc, T-motor Co., Ltd., China), LIDAR (Here flow, HEX Co., Ltd., China), Front Sensor (Tf Mini, Benewake Co., Ltd., China) and 13-inch propeller were considered as the main components of the control unit. Table 1 shows the weights of the main components of the control unit. The total weight of the main components of the control unit was 860.4 g.
The injection unit is composed of a water pump for spraying the control liquid, an ESC for controlling the injection amount, a nozzle for securing the spray area, and a control liquid tank which can hold a 500 ml capacity control liquid. We considered the water Pump, the ECS, and the spray nozzle as the main components of the injection unit. Table 2 shows the weights of the main components of the injection unit. The total weight of the main components of the injection unit was 422 g.
For the power supply unit, a 6-Cell Li-Polymer Battery (PT-B 6,300mAh POLY-TRONICS Co., Ltd., China) was used to supply the power required for the flight, control of the drone, and the spraying of the pest control liquid. The weight of the battery was 830 g.
Ⅲ. Design and Simulation
Greenhouses used domestically vary in size depending on the characteristics of each crop.
In this study, we designed a drone for use in a greenhouse measuring 8 m in width, 100 m in length, and 3 m in height. The exterior walls of the greenhouse were made up of vinyl and glass mostly, hence using large agricultural drones posed a risk that the propeller might damage the vinyl and glass. In particular, when cultivating fruits in greenhouses, drones cannot secure the height to fly due to the height of the tree. Therefore, drones used in enclosed spaces, such as, greenhouses must be smaller and lighter. Figure 2 shows the size of the greenhouse and the flight path of the drone in the greenhouse. Considering the height of the greenhouse and fruit trees, we designed the drone to be compact with a length of 650 mm and a height of fuselage, including the GNSS, of 300 mm so that the drone can fly safely. Looking at Figure 2-(b), the flight path of the drone for control in the greenhouse was 200 m per flight. In other words, if the drone flew at a velocity of 2 m/s, the total flight time would be 100 s. Therefore, considering that 200 ml of control liquid was sprayed per minute, 500 ml of control liquid would sufficiently cover one greenhouse. Therefore, to minimize the total weight of drones in flight, we designed a 500 ml control liquid tank. Figure 3 shows the blueprint of the drone and liquid tank.
The weight of the main components used in drones is 2,112.4 g. Therefore, the total weight of the drone was predicted to be about 3,900 g, considering the carbon plate, pipes, and liquid tank used for the fuselage of the drone. Reflecting the expected weight and size of the drone and the specs of the key components used, we conducted a simulation design to confirm the possibility and flight time of the drone. "E-calc Multi-Copter Design" was used for the design, and Fig. 4 shows the simulation conditions.
At the time of simulation design, the total weight of the fuselage, including the weight of the control liquid, was expected to be 3,900 g, and therefore we simulated by changing the weight of the fuselage to 3,800 g, 4,000 g, and 4,200 g. In the simulation, the frame size was fixed to 650 mm as in the drone external design. The maximum discharge rate of the 6-Cell Li-Polymer 6,000 mAh battery was set to 85%. Four Antigravity 4006-380 KV motors and four propellers with 13-inch diameter and 4.4-inch pitch from T-Motor Co. Ltd. were used. The tilt limit of the drone's FC was limited to 35°. The ESC was replaced with a product of the same performance because it was not supported by e-calc. Since the purpose of the drone is to control the inside of a small greenhouse, the height limit of the drone was set to 5 m and the indoor temperature was set to 40 °C.
Figure 5 shows the simulation results with the drone weight set to 3,800 g. The minimum flight time after fuselage took off was predicted to be at least about 6.9 minutes and it was confirmed that a sufficient flight time was secured with a weight of 3,800 g. The possible time for hovering was predicted to be about 10.4 minutes, and the combined time for hovering and flying was predicted to be 9.2 minutes. In addition, the maximum inclination was calculated to be 25° and the maximum flight velocity was calculated to be 26 km/h.
Figure 6 shows the simulation results with the drone weight set to 4,000 g. The minimum flight time after fuselage took off was about 6.9 minutes, the same as the 3,800 g fuselage.
Therefore, considering the flight time, the fuselage weighing 4,000 g was found to have sufficient flight time. The possible time for hovering was predicted to be about 9.6 minutes, and the combined time for hovering and flying was predicted to be 9.6 minutes. In addition, the maximum inclination was calculated to be 17° and the maximum flight velocity was calculated to be 18 km/h.
Figure 7 shows the simulation results with the drone weight set to 4,200 g. The minimum flight time after fuselage took off was predicted to be about 6.9 minutes, the same as the 3,800 g and 4,200 g fuselages. The possible time for hovering was predicted to be about 8.9 minutes, and the combined time for hovering and flying was predicted to be 8.1 minutes. However, the maximum inclination was calculated to be less than 5° but the maximum flight velocity was not calculated.
Table 3 shows the simulation results of changes in weight.
It was confirmed that the minimum flight time was 6.9 minutes even if the weight of the fuselage changed. The combined time for hovering and flying, excluding the minimum flight time, decreased with increasing fuselage weight. Since the estimated time to control a greenhouse is about 100 s, it was confirmed that sufficient flight time could be secured when manufacturing a drone using the main components proposed in this study.
When a drone flies while hovering, it moves while tilting in the direction of flight. At this time, the thrust is reduced proportionally to the angle of inclination, which affects flight safety, velocity and range, and the drone inclination is limited to 35°. In the simulation, the maximum inclinations were 25° at 3,800 g, 17° at 4,000 g, and 5° or less at 4,200 g, which did not exceed the maximum inclination limit. However, the maximum flight speed was 26 km/h at 3,800 g and 18 km/h at 4,000g, but the flight speed was not calculated at 4,200 g. The thrust value of the drone has a great influence on hovering and flying. To ensure flight safety, we designed the drone to avoid using the maximum throttle of the motor. As a result of simulation, the PWM throttle of the motor which enabled hovering at a weight of 4,200 g exceeded 80%. It means that the drone cannot hover unless it uses more than 80% of the throttle and can fly above that. Therefore, a drone weighing 4,200 g is expected to have difficulty flying due to the small difference between the thrust used for hovering and the maximum thrust used for transport due to the high PWM throttle. In the actual flight, if the external flow velocity resistance was reflected, the thrust value might be insufficient and the flight might become impossible. It is judged that the result of the flight velocity was not displayed on the simulation. Therefore, in order for the drone to fly in the greenhouse and control pest stably, it should be manufactured with a weight of 4,000 g or less.
Ⅳ. Conclusion
In this study, we designed a simulation for the development of a small drone for remotely controlling pest in a greenhouse. The total weight of the main components of the fuselage is 2112.4 g, and therefore, the drone to be used in the actual greenhouse was expected to weigh less than 3,900 g. To confirm if a drone weighing 3,900 g could actually fly and control pest, we simulated by changing the weight of the fuselage to 3,800 g, 4,000 g, and 4,200 g. As a result, at a weight of 3,800 g, the maximum inclination was predicted to be 25°, the combined flight time was 9.2 min, and the maximum speed was 26 km/h, and at a weight of 4,000 g, the maximum inclination was predicted to be 17°, the combined flight time was 8.6 min, and the maximum speed was 18 km/h. However, at 4,200 g, the difference between the thrust used for hovering and the thrust used for transport was small, and it was predicted that flight would be impossible. Therefore, it was proposed that the small drone used in greenhouses must be manufactured with a weight of less than 4,000 g to ensure flight time and safety. In addition, it is expected that if an automatic flight function, which can set a flight route is installed in the future, it will be possible to automatically control pest in the greenhouse even if there is no farmer.
Acknowledgments
This research was supported by the Dongshin University research grants. And the paper was a revised and supplemented of the first author's master's thesis.
References
- M. S. Choi, “A Study on the Efficient Implementation Method of Cloud-based Smart Farm Control System,” Journal of digital convergence, Vol. 18, No. 3, pp. 171-177, Mar. 2020.
- B. H. Shin and H. K. Jeon, “ICT-based Smart Farm Design,” Journal of Convergence for Information Technology, Vol. 10, No. 2, pp. 15-20, Feb. 2020.
- H. S. Kim, H. C. Kim, M. J. Kang and J. W. Jwa, “Data Processing and Analysis of Non-Intrusive Electrical Appliances Load Monitoring in Smart Farm,” Journal of IKEEE, Vol. 24, No. 2, pp. 632-637, Feb. 2020.
-
S. Y. Min, J. B. Jeon, M. J. Lee and W. Oh, “Analysis of Environments in Smart Greenhouses as Influenced by Cultivation Method of Cut Roses,” Flower Research Journal, Vol. 28, No. 4, pp. 340-346, Oct. 2020.
[https://doi.org/10.11623/frj.2020.28.4.13]
- S. H. Kim, T. H. Lee, Y. M. Han and H. J. Byun, “A Study on the Design and Implementation of Multi-Disaster Drone System Using Deep Learning-Based Object Recognition and Optimal Path Planning,” KTCCS, Vol. 10, No. 4, pp. 117-122, Apr. 2021.
- M. W. Son, Y. T. Ju, J. S. Kim and E. K. Kim, “Multi-Purpose Integrated Training Drone to Prevent Safety Accidents,” The Journal of the Korea Institute of Electronic Communication Sciences, Vol. 16, No. 1, pp. 145-150, Feb. 2021.
- S. H. Yoo, Y. T. Ju, J. S. Kim and E. K. Kim, “Design and Development of Underwater Drone for Fish Farm Growth Environment Management,” The Journal of the Korea Institute of Electronic Communication Sciences, Vol. 15, No. 5, pp. 959-966, Oct. 2020.
- S. K. Kim, D. Y. Lim and S. Y. Jung, “Low Cost Evaluation Method of Agricultural Drone with Simulated Spraying System,” J. Adv. Eng. and Tech, Vol. 12, No. 2, pp. 77-84, Jun. 2019.
- J. T. Lim, “A Study on the Characteristic Analysis of the Pest Control Drones Using Smart Operating Mode,” Journal of Convergence for Information Technology, Vol. 9, No. 10, pp. 108-113, Oct. 2019.
- J. T. Lim, “Development of Spray Calculation Algorithm Using the Pest Control Drones,” Journal of Convergence for Information Technology, Vol. 10, No. 10, pp. 135-142, Oct. 2020.
- I. S. Shin and K. S. Choi, “An Analysis of agricultural Drone Use Using News Big Data: Focusing on the Agricultural Cooperative’s Pest Control Project,” Cooperative Economics and Management Review, Vol. 52, pp. 61-80, Jun. 2020.
2021년 : 동신대학교 대학원 전기전자공학과 석사과정
1995년 : 동신대학교 전자공학과 졸업 (공학사)
1995년~현 재: 보성군청
※관심분야:디지털콘텐츠 시스템, 콘텐츠 응용 및 기타 융합기술, 융합콘텐츠, 의료영상, 의공학, 3D 모델링 등
2003년 : 동신대학교 대학원 (공학석사)
2006년 : 동신대학교 대학원 (공학박사-전기전자공학)
2008년 : 조선대학교 대학원 (의학박사-외과학)
2006년~2008년: ㈜바이오아테코
2008년~2010년: ㈜에코레이
2010년~현 재: 동신대학교 보건행정학과 교수
※관심분야:디지털콘텐츠 시스템, 콘텐츠 응용 및 기타 융합기술, 융합콘텐츠, 의료영상, 의공학, 3D 모델링 등